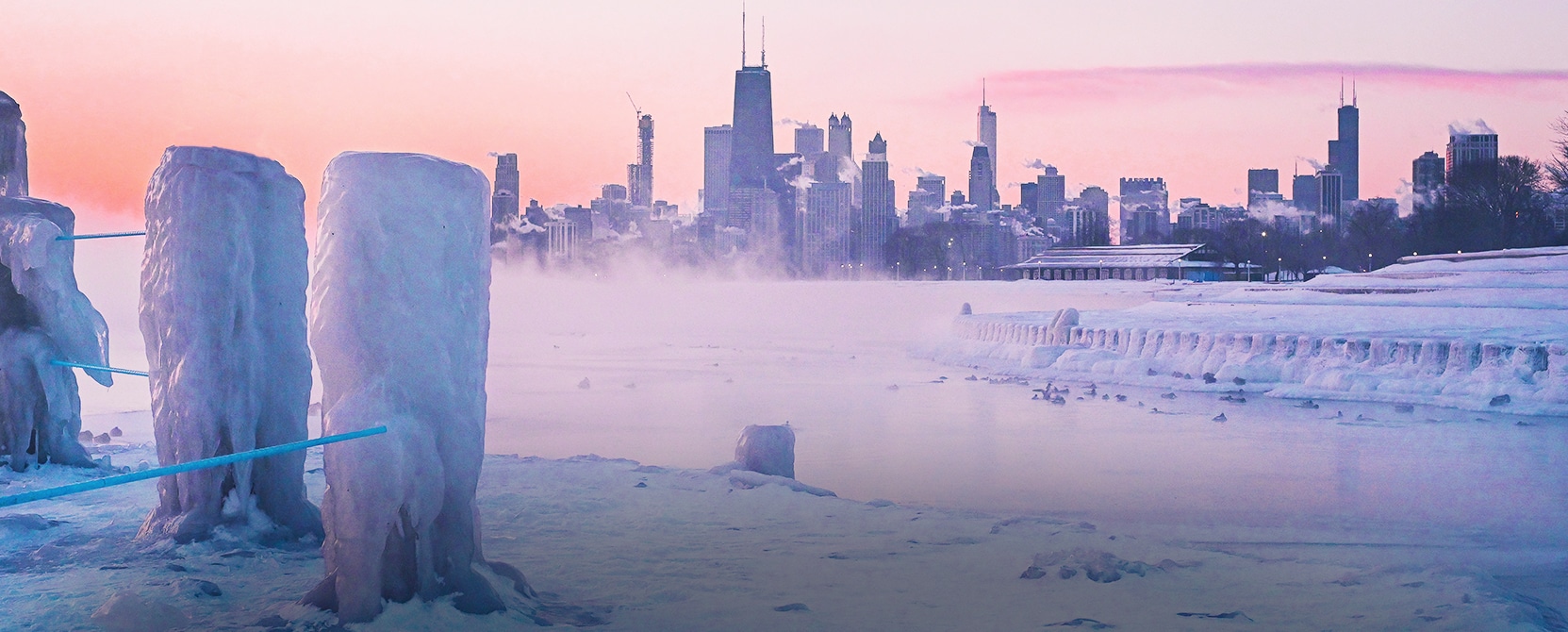
For a customer from Bavaria, Militzer & Münch Germany is handling a project – the volume of the order: 200 to 250 containers. Over several months, the team is transporting façade components and construction material from Bavaria to an American chemical plant near Chicago. In January, an extreme cold wave caused a state of absolute emergency in the USA – and posed quite some challenges to the team.
A chemical plant in Chicago is being expanded at this time. In late 2018, a Bavarian manufacturer contracted Militzer & Münch to deliver the necessary façade components and building material from Germany to the USA. The project is scheduled to be finished by spring 2020.
Up To Seven Containers Per Week
So how do over 200 heavy-weight containers get from Bavaria to Chicago? “This is of course a big project”, says Walter Weissig, Manager Ocean Freight and Deputy Branch Manager at M&M air sea cargo GmbH in Munich. “First of all, we negotiated the tariffs, the potential routes and dates with the shipping line and their trucker, and closely coordinated with our Hamburg colleagues and our partner in Chicago.”
The freight for the American customer consists mainly of 40’ HC containers and some 20’ standard boxes. All in all, the team prepares five to seven containers for transport each week, some of them weighing up to 19 tons.
“After we have loaded the containers at the exporter’s location in Lower Bavaria, the first leg of the transport is via rail to Bremerhaven”, says Walter Weissig. “From there, we ship the cargo to New York or Norfolk. The shipping line is then in charge of rail transport to the destination hub at Chicago / Norfolk Southern Landers. The last leg to consignee is done by truck.”
Icy Cold Winters and Extreme Situations
In January, a sudden cold wave hit the United States. “The polar winds caused temperatures last winter to drop as far as minus 30°C”, says Walter Weissig. “That was the second lowest value ever registered in the USA.”
Between New York and Chicago, there reigned an absolute state of emergency. “Containers were stuck up to two weeks at the port, before they were trucked to New Jerseys where they were put on rails”, says Walter Weissig. “What’s more, there is this lack of drivers in the USA. The customer of course insists on exact delivery times with the appropriate advance notice. This is not always easy to manage, as on the day the container reaches Chicago, we don’t yet know which driver is assigned for the last mile.”
Going For It, With Full Commitment
Daily reconciliation of all shipments via tracking and tracing and via mail is indispensable. “With up to 30 containers at the same time with different status reports – loaded at shipper’s warehouse, shipped on board, vessel arrival New York / Norfolk, discharged, transit to rail, rail departure, train arrival, picked up for delivery, delivery – this is extremely time-consuming”, Walter Weissig says. “In the meantime, the transport chain has become established. Due to good cooperation between the shipping line, our agent and the customer, everything runs smoothly. Overall transit time is 30 days maximum.”
The Militzer & Münch team is already working on a follow-up project. The Bavarian shipper has enquired about the transport of another sixty to seventy 40’ containers. The consignee: another company, also in the United States.